How Strong Are 3D Printed Parts?
- Kristaps Rozenbergs
- 8. apr.
- Lasīts 6 min
Updated: 27. apr.
In recent years, 3D printing has grown from a basic prototyping method into a powerful tool for mechanical design and manufacturing. It's now used to produce parts for aerospace, automotive, machinery, and custom tools. But how strong are 3D printed parts in real-world conditions? Can they truly replace parts made with traditional manufacturing methods?
The strength of 3D printed parts depends on several key factors: the material used, the printing method, how the part is designed, and how it's finished after printing. In this article, we'll take a closer look at each of these areas.
How Strong Are 3D Printed Parts: Factors That Affect Durability
The durability of 3D printed parts varies based on material, printing technology, design, and post-processing.
Let’s explore these aspects in this article.
1. Material Selection
How strong are 3D printed parts?
Different 3D printing materials offer different properties.
Some materials provide greater durability, while others offer less. Some are more flexible, whereas others are not.
For example:
Polylactic Acid (PLA) is easy to print but can be brittle, making it unsuitable for high-stress situations. However, PLA prints quickly, maintains detail effectively, and experiences minimal warping. It is often used for product design mockups, architectural models, scale models, and non-functional engineering prototypes. PLA is often used in creating light-duty household items and decorative objects.
ABS and PETG provide good impact resistance and heat tolerance. These materials are more durable and heat-resistant than PLA, making them better suited for functional, mechanical, or outdoor parts. PETG are often used in making flexible but tough parts such as hinges, clips, snap-fit joints, bike accessories. ABS, however, are prefect for creating various consumer products (like keyboard keycaps, phone cases, protective covers) and tools (drill guides, templates, fixtures).
Nylon, polycarbonate, and carbon-fiber-reinforced composites are among the best materials for 3D printed parts. These are much stronger and more flexible, making them ideal for functional mechanical uses. These high-performance filaments excel in challenging, real-world mechanical scenarios where strength, flexibility, and durability are essential. Drone frames, industrial machinery components, structural reinforcements, connectors and fittings, and bicycle parts (such as pedals and handlebars) are often constructed from nylon, polycarbonate, and carbon-fiber-reinforced composites.
Metal 3D printing using materials like titanium or stainless steel can produce parts with strength that matches or exceeds that of conventionally machined metal components. These 3D printed metal parts closely resemble traditionally machined or cast metal in both appearance and performance. Metal 3D printed parts are utilized in engine components, heat exchangers, custom exhausts, brackets, robotics, and automation. 3D printed aluminum parts are part of metal 3D printing, too. Aluminum is commonly used in metal 3D printing due to its lightweight properties, strength, and corrosion resistance. If strength is your priority, metal is the best material for 3D printed parts.
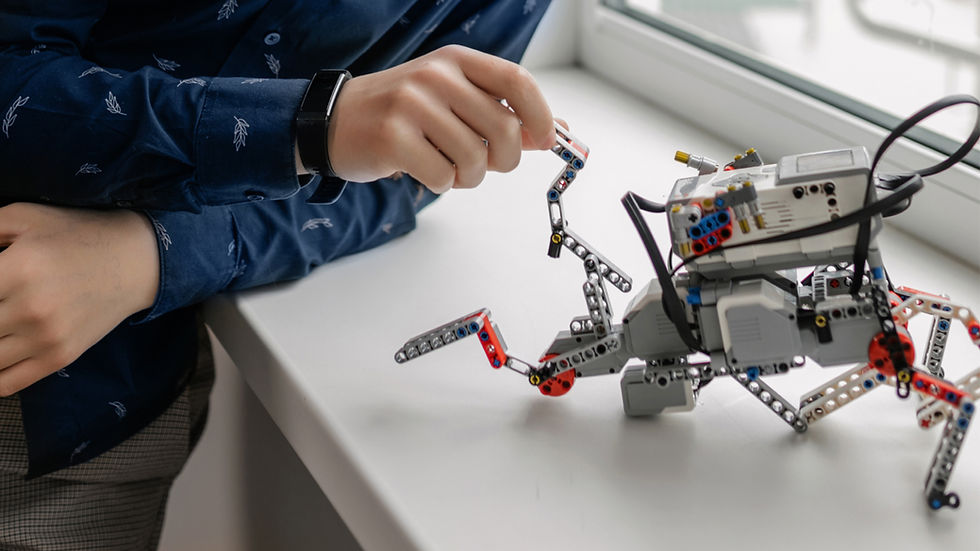
1.1 What Is the Best Material for 3D Printed Parts?
The best material for 3D printed parts depends on the intended use, but some materials are notable for their mechanical properties.
Polycarbonate is among the strongest and most heat-resistant materials, making it suitable for load-bearing parts, protective equipment, and high-performance components, although it requires a high-temperature printer.
Nylon is also a great option for durable, flexible parts such as gears, hinges, and drone components due to its abrasion resistance and ability to withstand stress. For parts that need to be strong yet lightweight, carbon-fiber-reinforced composites provide excellent stiffness and dimensional stability, making them ideal for use in robotics, automotive, and aerospace fields.
When ultimate strength and heat resistance are needed, metal 3D printing with materials such as stainless steel, titanium, or Inconel is the preferred option, albeit costly and necessitating specialized equipment.
PETG serves as a suitable compromise for functional parts that demand weather resistance and durability, like outdoor mounts or containers, and it is simpler to print compared to materials like nylon or PC.
For beginners or non-functional items such as prototypes and models, PLA is the preferred material due to its ease of use and decent print quality, despite its lack of strength and heat resistance.
When evaluating the strength of 3D printed parts, it's also crucial to recognize the wider benefits of 3D printing, including speed, design flexibility, cost-effectiveness and reduced material waste.
Overall, for serious mechanical applications, materials like polycarbonate, nylon, carbon-fiber composites, and metal offer the best performance, while PETG and PLA are better suited for general-purpose or simpler needs.
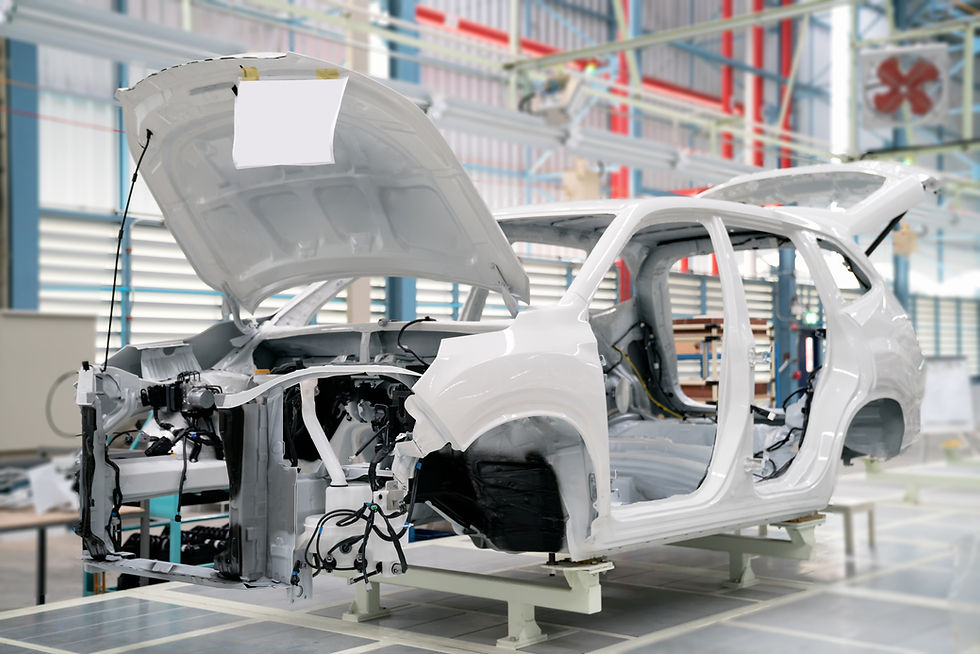
2. Printing Technology
How strong are 3D printed parts?
The type of 3D printing technology also significantly influences durability:
FDM (Fused Deposition Modeling) parts may suffer from weak inter-layer adhesion, leading to delamination under stress. This occurs due to the layer-by-layer extrusion of thermoplastic filament, where bonding can be insufficient if printing parameters like temperature, speed, or layer height are not optimized. This is critical for parts requiring high strength, necessitating design strategies to enhance adhesion, such as increasing layer contact area or using materials that improve bonding.
SLA (Stereolithography) provides excellent surface finish but can be brittle. It uses a laser to cure liquid resin, producing detailed and smooth parts. However, these parts often lack toughness, posing a drawback for applications needing impact resistance. Users should consider the intended use and may need to incorporate design features or select resins that enhance durability.
SLS (Selective Laser Sintering) and MJF (Multi Jet Fusion) offer isotropic properties and superior mechanical strength through powder bed fusion. This process creates parts with uniform density and strength in all directions, ideal for functional prototypes and end-use parts. These methods support various materials and complex geometries without support structures, enhancing versatility and efficiency.
DMLS (Direct Metal Laser Sintering) and other metal additive manufacturing methods produce highly durable metal parts with near-forged quality. DMLS uses metal powders to create intricate components with exceptional mechanical properties, suitable for demanding applications in aerospace, automotive, and medical industries. This process reduces material waste and allows for lightweight, complex structures, improving performance. Advances in DMLS enhance surface finish and accuracy, approaching the quality of forged components.
3. Design Considerations and 3D Print Orientation
3D printing provides exceptional design flexibility, enabling the creation of customized, efficient parts while minimizing material use, part weight, and production costs. This advantage is especially valuable in industries where weight reduction is critical, such as aerospace and medical sectors.
However, it's important to remember that 3D print orientation can impact 3D printed part's strength.
The orientation during the process can create weak points, especially in methods like Fused Deposition Modeling (FDM). In FDM, the strength of the part depends on how well the layers bond together. If the layers are aligned perpendicular to the applied stress, they may not bond strongly enough, leading to delamination or failure. This is especially problematic under high stress or twisting forces, where the layers can separate.
To minimize these issues, careful attention must be paid to 3D printing orientation during printing. Using advanced slicing software, adjusting orientation, and adding support structures can help improve strength. Post-processing techniques like annealing or curing can also enhance the mechanical properties of 3D printed parts.
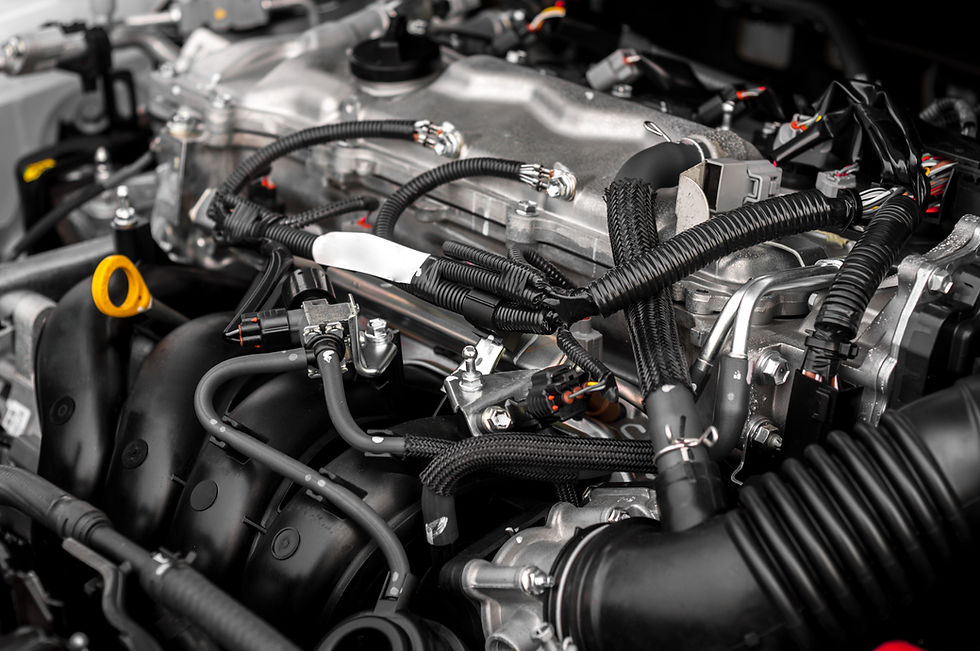
4. Post-Processing
Post-processing plays an important role in enhancing the attributes of 3D printed parts, particularly in boosting their durability, strength, and overall functionality. Once a part is printed, finishing techniques like annealing, infiltration, and the incorporation of metal inserts can greatly enhance its mechanical performance, making it fit for demanding applications.
Heat treating is among the most prevalent post-processing techniques for metal 3D prints. This involves exposing the printed part to controlled high temperatures, which helps alleviate internal stresses that may have formed during printing, potentially causing warping or cracking. Heat treating also enhances the material's structural integrity by modifying its microstructure, improving properties such as strength, toughness, and hardness. In metal 3D printing, this process is frequently employed to optimize the final part for its intended use, whether in aerospace, automotive, or industrial settings.
Infiltration is another post-processing method, especially beneficial for porous or hollow 3D printed parts. This technique involves introducing a secondary material (often metal or resin) into the part to fill voids or pores left during printing. This increases the part’s density, strength, and durability. Infiltration can also enhance the part’s surface finish and reduce porosity, making it more resistant to wear and tear, which is crucial for parts exposed to high pressure or extreme conditions.
Moreover, metal inserts can be added during post-processing to strengthen specific areas of a part that may need additional reinforcement or functionality. These inserts, typically made from materials like steel or aluminum, are incorporated into the 3D printed part to boost its load-bearing capacity, thermal conductivity, or wear resistance. This technique is particularly beneficial in applications where certain components experience higher stresses.
Additional post-processing techniques, such as polishing, sandblasting, and coating, can further improve the part’s surface finish and appearance, while also enhancing its resistance to corrosion or environmental factors. These finishing steps not only enhance the part’s functionality but also increase its aesthetic appeal, making it more suitable for consumer-facing applications.
Please note that Perfecttio does not currently provide post-processing services. Parts are delivered exactly as they are produced by the 3D printer, without additional finishing.
By understanding these key factors, you can unlock the full potential of 3D printing for strong, reliable parts. Whether you're prototyping or ready for production, our team is here to help you bring your ideas to life with precision and performance. Contact us for more information!